A CMMS comes with multiple advantages for companies seeking to improve their maintenance processes. Here’s a list of the top CMMS benefits:
1. Enhanced Maintenance Scheduling
The automated nature of a CMMS means factories, manufacturing plants, production facilities and other related businesses can improve task performance tracking and productivity. That’s because scheduling is streamlined for the full range of maintenance tasks in the pipeline – from assigning the right specialist to the job to knowing when the right time for a certain machine’s maintenance session is.
2. Reduced Machine Downtime
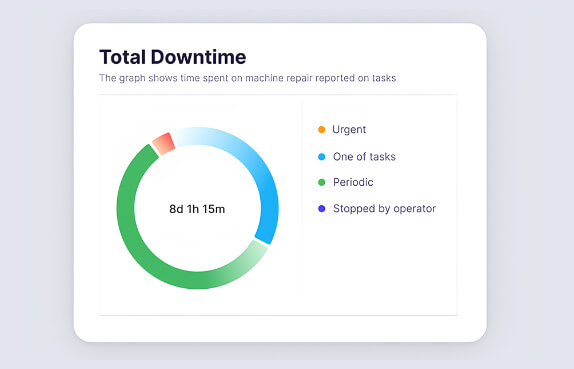
Machines that break down unexpectedly can cause costly problems for the organization. These include lost labor hours, waiting for parts to be delivered (if they are not stocked) and halted production processes. Automated preventive and predictive maintenance greatly facilitate repairs and inspections. The maintenance department can set up triggers indicating when machines should be serviced before they reach the point of breakdown. This ensures optimal uptime for all equipment.
3. Efficient Work Orders
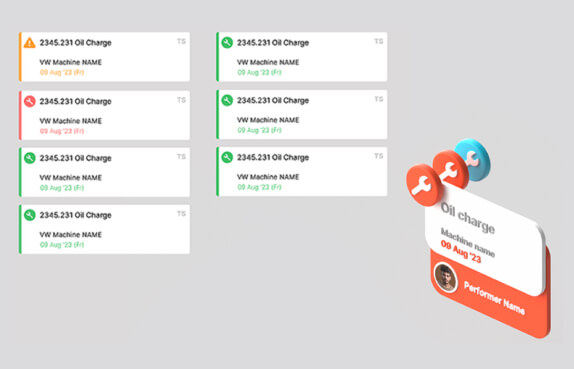
Many production plants and factories still rely on paper-based records, Excel spreadsheets and verbal instructions. With an automated maintenance work order process, every team member’s skills are utilized as efficiently as possible. The right specialist is allocated to a task at the right time. A reduction in paperwork and manual sorting is an additional benefit.
Discover the long-term benefits of planned preventive maintenance, which contribute to reduced machine downtime and efficient work orders.
4. Simplified Record-Keeping
A CMMS offers a centralized database where authorized team members can access every detail about every machine. When technicians input data for a completed repair task, the database automatically updates. The platform synchronizes the number of spare parts left in inventory. It also keeps a record of what type of maintenance was carried out on the machine and when. So tracking the entire maintenance process becomes much more efficient.
5. Reduced Knowledge Load on Technicians
Uploading relevant images and guides along with the work order accelerates the maintenance process. Technicians have access to all important information, including procedural documentation and previous maintenance records.
6. Data Collection
The large CMMS database is not only procedural but also analytical. It can produce live reports that provide key metrics and insights to facilitate decision-making. Furthermore, a CMMS enables a decision-maker to access historical data. This helps optimize maintenance activities and identify patterns and areas for improvement.
The data collection capabilities of a maintenance system are extensive, allowing you to generate informative reports. Check out some insightful CMMS report examples.
7. Compliance With Regulations
In addition to their internal regulations, production facilities must also adhere to external regulatory obligations. Examples include following ISO standards to meet industry demands. Using CMMS makes the auditing process smoother because its data-tracking capabilities can prove compliance with regulatory requirements. The system gives real-time access to a digital maintenance backlog record.
If you want to learn about the latest CMMS software trends, read our article on this topic. It's full of insights about the future of maintenance operations.