The management of maintenance is a critical component for the success of any modern manufacturing company. It ensures the safety, reliability, and efficiency of production processes by supporting the continuous operation of equipment and minimizing downtime. In the context of increasing global competition, heightened quality requirements, and the necessity to comply with international standards, the significance of effective maintenance grows.
Historical Context and Evolution of Maintenance in Manufacturing
The history of industrial maintenance began with a simple, reactive form, where equipment was repaired only as needed. With technological advancements and changes in production paradigms, maintenance has undergone significant development. In the 20th century, society shifted toward preventive maintenance, where technology began to play an important role in diagnosing and servicing machinery. European-Bulgarian standards and integration with international partners stimulated the adoption of modern approaches such as predictive and proactive maintenance.
Introduction to Modern Challenges and Opportunities
Today's industry faces numerous challenges—from rapidly evolving technologies to increasing environmental and regulatory demands. Effective maintenance management requires the integration of modern technological solutions such as the Internet of Things (IoT) and Artificial Intelligence (AI), which provide new opportunities for innovation and optimization. Developing strategies that balance traditional methods with innovative technologies is key to sustainability and success.
Detailed Explanation of the Term "Maintenance Management"
"Maintenance Management" describes the system of processes and activities aimed at ensuring the continuous and effective operation of equipment. This encompasses not only routine repair activities but also a comprehensive management strategy that includes diagnostics, planning, resource allocation, and process optimization. The primary goal is to extend the asset lifecycle and improve resource efficiency.
Importance of Maintenance for Business and Its Impact on Efficiency and Safety
Effective maintenance management is essential for ensuring high efficiency in production processes and maintaining a safe working environment. Insufficient maintenance can lead to unplanned downtimes, accidents, and increased costs, significantly impacting the economic performance of a business. Workplace safety must also be taken seriously—preventing accidents and incidents through regular maintenance is crucial for avoiding human and financial losses.
Maintenance-Related Costs and the Economic Impact of Ineffective Maintenance
Maintenance is a significant part of the budget for any manufacturing enterprise. Costs include both direct repair expenses and investments in technology and staff training. Ineffective maintenance can lead to substantial costs associated with emergency repairs and productivity loss, which can be mitigated through strategic maintenance approaches. Cost analysis shows that investing in preventive and predictive maintenance often leads to significant long-term savings.
Reactive Maintenance: Advantages and Disadvantages
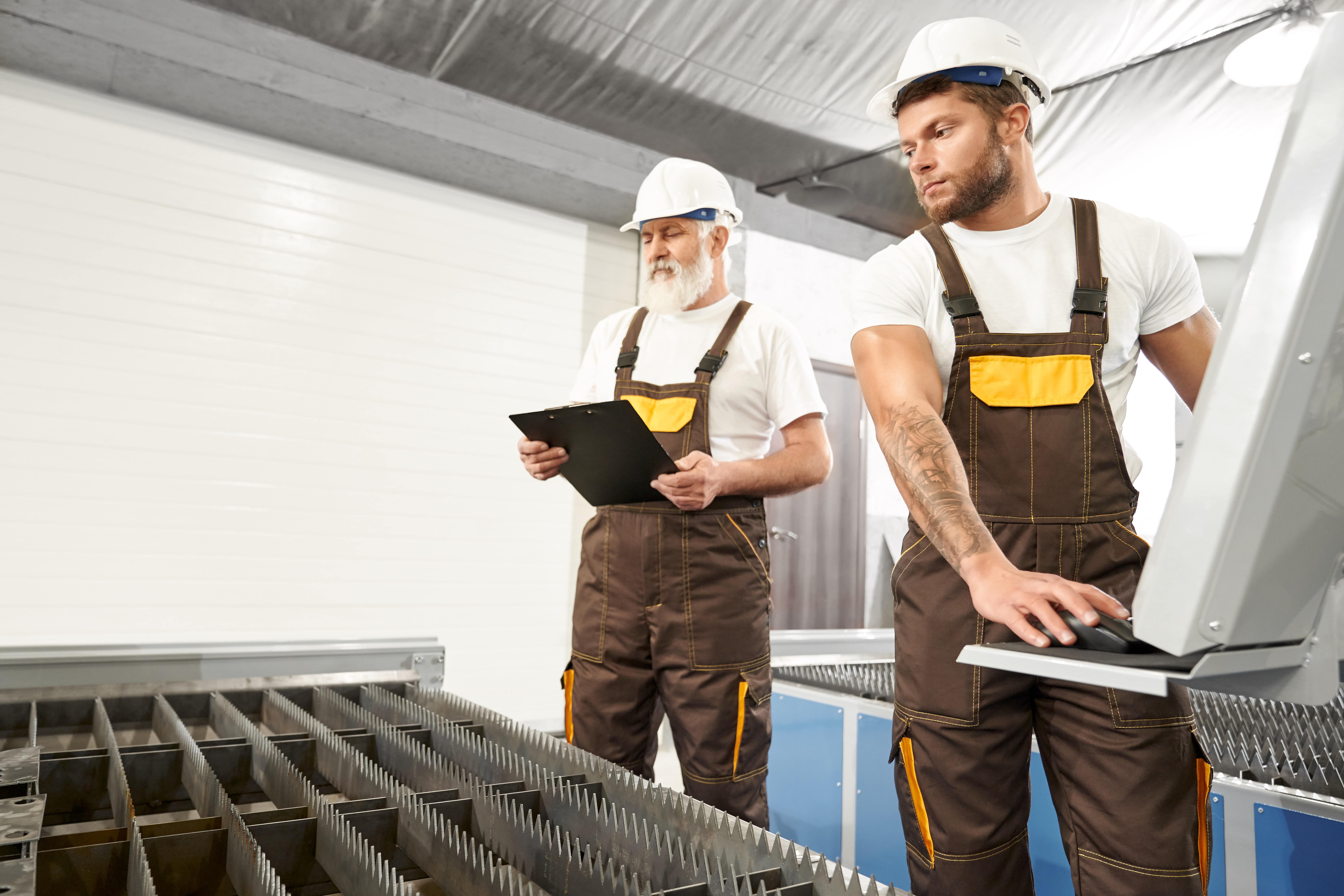
Reactive maintenance, also known as "run-to-failure" or "breakdown" maintenance, is based on the concept of intervention only after equipment failure occurs. This is perhaps the oldest and most traditional approach to maintenance, applicable in situations where immediate response after malfunction is possible and does not lead to significant losses.
Advantages:
- Simplicity in planning, as actions are taken only when a problem arises.
- Minimal immediate costs for maintaining equipment, since there are no planned activities until failure occurs.
- Can be suitable for less critical systems that do not seriously affect overall production.
Disadvantages:
- Potentially high costs due to unplanned interruptions and emergency repairs.
- Possible damage to reputation due to delays in the production process.
- Increased risk to safety and the environment if failures occur in critical facilities.
Preventive Maintenance: Strategies and Industry Examples
Preventive maintenance is an approach in which maintenance activities are performed periodically to prevent failures. This approach is often time-based or usage-based, aiming to avoid unexpected downtimes and increase equipment reliability.
Strategies:
- Developing a routine inspection and maintenance schedule that covers all critical components of the equipment.
- Using manufacturer standards and recommendations for scheduling maintenance activities.
- Including staff training related to inspections and maintenance of specific equipment.
Industry Examples:
- In the automotive industry, preventive maintenance is standard for oil changes on vehicles after a certain mileage.
- In energy, distribution networks often utilize preventive maintenance to check and replace components to prevent failures.
Predictive Maintenance: Technologies and Implementation Methods
Predictive maintenance is based on monitoring the condition of equipment and utilizes data from various sensors and systems to analyze it. Through technologies such as the Internet of Things (IoT) and data analytics, companies can predict when a failure will occur and take necessary actions before it happens.
Technologies:
- IoT devices that collect data from sensors to deliver real-time information on equipment status.
- Data analytics software that uses artificial intelligence or machine learning to predict the likelihood of failures.
Implementation Methods:
- Integrating sensors at all critical points of machines to ensure a continuous flow of data.
- Using cloud platforms for processing and storing large volumes of data.
- Developing predictive models that can be trained and adapted based on real-time conditions and operational data.
Proactive Maintenance: Identifying and Addressing Root Causes
Proactive maintenance aims not only to anticipate and prevent failures but also to analyze and eliminate the root causes of their occurrence. By applying this approach, organizations can reduce the risk of problems occurring and increase the lifecycle of assets.
Identifying Causes:
- Conducting failure analysis and collecting data to investigate root causes.
- Utilizing techniques such as root cause analysis (RCA) to understand the mechanisms of failures.
Addressing Causes:
- After conducting analyses, correcting processes or equipment design to avoid recurring issues.
- Incorporating proactive measures in daily practices, such as changing operational procedures or updating equipment with the latest technologies.
IoT and AI in Maintenance: How They Are Changing the Way of Working
With the advancement of technology, the Internet of Things (IoT) and artificial intelligence (AI) are having a significant impact on maintenance management. IoT devices equipped with sensors collect and transmit real-time data, allowing specialists to have constant access to information about equipment status. This enhances the predictive capability of organizations, enabling them to identify potential problems even before they arise.
AI algorithms analyze this data and provide valuable insights that help optimize processes and facilitate informed decision-making. For instance, in recent years, AI has been used to understand complex patterns and detect anomalies in large data sets, significantly reducing the need for human intuition and errors.
CMMS Systems: Functionalities and Benefits
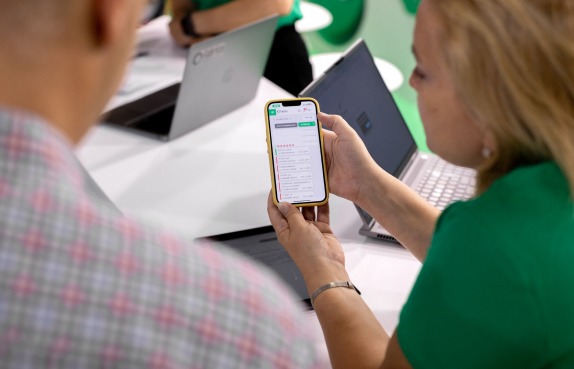
Computerized Maintenance Management Systems (CMMS) are powerful tools that transform the way assets and processes are managed. CMMS systems provide centralized access to the information needed for effective maintenance planning and resource management. They facilitate the collection and analysis of asset data, supporting decision-making processes and optimizing planned and emergency repairs.
Functionalities:
- Managing work orders and maintaining a history of performed activities.
- inventory management that helps optimize inventory control.
- Maintenance planning and inspection scheduling.
- Generating reports on maintenance performance and costs.
Benefits:
- Reduction of downtime and increased productivity.
- Improved resource and inventory management.
- Enhanced communication and collaboration among different departments.
- Compliance with regulatory requirements and maintaining workplace safety.
Automation and Digitization in Maintenance
Automation and digitization play a central role in transforming maintenance. By automating repetitive tasks such as maintenance scheduling, data collection, and condition monitoring, enterprises can save time and reduce operational costs. Automation technologies include robotic systems that can perform hazardous tasks or those requiring a high degree of precision.
Digitization:
Digitization involves implementing digital technologies to enhance the management and control of maintenance. This includes using cloud platforms for data storage and analysis, as well as mobile applications that allow technicians to receive up-to-date information directly on their devices.
Impact on Operations:
Automation and digitization improve the transparency and efficiency of maintenance processes while allowing for the avoidance of human errors. They also provide the opportunity for more flexible and timely responses to emergency situations, which is essential for maintaining competitiveness.
Structuring Maintenance Departments in Companies
An effective structure for maintenance departments is key to the successful management of a company's assets. A well-structured department should ensure a clear distribution of responsibilities and effective communication between team members and other departments. The main components to consider when structuring a maintenance department include:
- Functional teams: Specialized groups responsible for specific types of maintenance or equipment.
- Leadership roles: Appointing leaders or managers to coordinate the efforts of individual teams and share information with management.
- Communication and coordination: Establishing systems for information sharing and developing procedures for reporting and feedback.
- Training and development: Investing in regular training to ensure personnel are familiar with modern technologies and methods.
Change Management and Implementation of New Systems and Practices
Implementing new systems and practices in maintenance management often requires a well-managed change program. Change management is a process that facilitates the transition from existing to new methods of operation with minimal disruptions to daily activities. Key steps in change management include:
- Needs analysis and planning: Understanding and defining areas for improvement.
- Communication and engagement: Ensuring clear and transparent communication about changes and involving personnel in decision-making.
- Training and support: Providing necessary resources and training for staff to adapt to the new systems.
- Monitoring and feedback: Regularly evaluating implemented changes and collecting feedback for potential adjustments and improvements.
The Role of Leadership and Management in Effective Maintenance
Leadership is an important component of successful maintenance management. Good leaders not only implement new practices and systems but also inspire and motivate their teams. The role of management in the context of maintenance includes the following aspects:
- Vision and strategy: Develop a long-term maintenance strategy that aligns with business goals and adapts the organization to changing conditions.
- Talent training and development: Identifying skill needs and promoting the professional development of staff.
- Willingness to innovate: Encouraging innovation and the use of technologies to improve efficiency and productivity.
- Maintaining sustainability: Building a culture of quality and safety within the organization to sustain long-term system functioning.
Importance of Cultural Changes in Adopting New Practices
Cultural changes in organizations are a crucial factor for the successful adoption and implementation of new technologies and methods in maintenance management. They involve changes in thinking, behavior, and attitudes of employees towards work processes. For successful adoption of new practices, organizations must create a culture that encourages:
- Innovation and Flexibility: Organizations should maintain an open environment for innovations in which employees are motivated to propose ideas and solutions.
- Collaboration: Effective communication and teamwork between departments are key to successfully implementing changes.
- Commitment and Responsibility: Employees should feel engaged and responsible for their actions and the outcomes of the organization.
Example strategies include regularly gathering feedback from staff, creating initiatives for sharing successes and challenges, and involving leaders in the change process.
Training and Development of Staff for Skill Enhancement
Staff training and development are critical for adapting to new technologies and methods. Skilled personnel are better prepared to cope with challenges and changes in the industrial environment. Key elements of effective training programs include:
- Ongoing Training: Establish continuous programs to update knowledge about the latest technologies and industry practices.
- Practical Experience: Encouraging learning through hands-on work and practical tasks that help employees apply what they have learned in practice.
- Passive and Active Learning: Balancing traditional training methods with active participation in simulations and role-playing exercises.
Companies can also invest in online courses and certifications for their staff to upgrade their skills and synchronize them with technological advancements.
The Relationship Between Staff Qualifications and Maintenance Efficiency
There is a clear relationship between the level of staff qualifications and the efficiency of maintenance. Trained employees can more effectively and quickly identify and resolve issues, leading to greater equipment reliability and less downtime. Studies show the following advantages of a highly skilled workforce:
- Reduced Response Time: Trained technicians are faster at diagnosing and fixing faults.
- Increased Efficiency: A better understanding of processes and equipment allows employees to optimize maintenance costs and time.
- Enhanced Safety: Trained employees are more aware of safe practices and potential risks, leading to a decrease in workplace incidents.
Organizations that invest in the qualification of their personnel often see reduced maintenance costs and increased productivity.
Methodologies for Assessing the Economic Benefits of Maintenance
Properly assessing the economic benefits of maintenance is crucial for understanding its value to the business and for optimizing investments. Several methodologies can assist in such assessments:
- Life Cycle Cost Analysis (LCCA): Involves analyzing the total costs of assets from acquisition to disposal. This analysis calculates maintenance, operational, energy, and end-of-life costs. LCCA provides a comprehensive view of the long-term costs and benefits associated with specific assets.
- Cost-Benefit Analysis (CBA): Evaluates economic efficiency by comparing the value of benefits and costs associated with specific maintenance activities. CBA helps determine the financial benefits of increased reliability and reduced downtime.
- Return on Investment (ROI): Calculates the return on a specific maintenance investment by comparing profit with costs. ROI can be useful for assessing the effects of implementing new technologies or training programs.
- Comparative Analysis: Involves comparing current levels of costs and productivity with industry standards and best practices. This method can help identify areas for improvement and optimize resources.
Capital Investments in New Maintenance Technologies
Investing in new maintenance management technologies often involves high initial costs but can lead to significant long-term savings. These investments include:
- Computerized Maintenance Management Systems (CMMS): Implementing CMMS can provide high efficiency in the planning and execution of maintenance activities. To assess the economic benefits, one can look at indicators such as reduced downtime and savings on maintenance costs.
- Internet of Things (IoT) and Sensor Technologies: By using IoT for condition monitoring, companies can enhance predictive maintenance and reduce operational interruptions. IoT systems allow businesses to collect data and make better-informed decisions that ultimately improve productivity and reduce costs.
- Using Artificial Intelligence (AI) and Machine Learning: AI and machine learning can offer real-time data analysis, predict failures, and optimize maintenance planning. The value of these technologies lies in their ability to extract additional value from existing resources and data.
- Mobile Technologies and Digitization: Mobile applications and digitization facilitate access to maintenance information and enhance operational flexibility. They also improve communication and efficiency among technicians, which can reduce overall costs.
Analysis of Successful and Unsuccessful Industry Examples
Successful Examples:
A Manufacturing Company in the Automotive Industry:
- Context: The company implemented preventive maintenance and used CMMS for tracking and planning maintenance.
- Outcome: After years of reactive maintenance, the company managed to reduce downtime by 30% and increase productivity by 15%. The implementation of automated systems allowed for faster identification of maintenance needs and optimization of inspection schedules.
- Key Elements: Planning, technological integration, and building a culture of prevention.
An Energy Company Using IoT:
- Context: The company integrated IoT sensors into its energy supply systems to monitor weather, vibrations, and temperature.
- Outcome: Thanks to real-time data, the company reduced emergency situations by 25%. The team improved foresight and resource management.
- Key Elements: Investment in IoT, data analysis, and strategic maintenance.
Unsuccessful Examples:
1. A Chemical Plant with Non-Strategic Approaches:
- Context: The plant relied on traditional reactive approaches with a minimal maintenance budget.
- Outcome: The lack of preventive and predictive maintenance led to a serious industrial incident causing significant economic and environmental damage.
- Lessons: The need for alertness to change, alignment with industry standards, and investment in preventive infrastructure.
A Heavy Equipment Manufacturer with Delayed Digitization:
- Context: Despite implementing CMMS, the company failed to integrate mobile technologies and AI functionalities.
- Outcome: The delay in digitization led to uncompetitive operations and loss of market share.
- Lessons: The importance of continuous technological advancement and applying modern solutions in maintenance.
Lessons and Conclusions for Effective Maintenance Management
- Culture of Prevention and Continuous Optimization: Successful cases show that companies that create an inseparable culture of preventive maintenance are often more capable of avoiding major incidents and optimizing their operations. Planning and training are critical for ensuring success.
- Importance of Data and Technologies: The implementation of modern technologies like IoT, AI, and CMMS plays a key role in increasing efficiency and reducing costs. These technologies not only provide accurate information but also opportunities for autonomous decision-making.
- Flexibility and Adaptability: Businesses must be flexible and ready to adapt to new conditions and technologies. Delayed reactions to innovations can lead to significant losses.
- Strategic Vision and Leadership: Visible leaders who implement a strategic vision for maintenance can inspire their teams to seek effective solutions and collaboratively overcome industry challenges.
Summary of Key Points
Maintenance management in modern industry is a strategic and complex process aimed at optimizing the performance and efficiency of production assets. The key elements we discussed include:
- Importance of Maintenance: Ensuring equipment safety and reliability, minimizing downtime, and optimizing asset management costs.
- Types of Maintenance: Considering various approaches such as reactive, preventive, predictive, and proactive maintenance. Each has its own advantages and challenges and should be tailored to the specific needs and conditions of the organization.
- Technologies and Automation: Implementing IoT, AI, and CMMS systems significantly enhances maintenance management through real-time data analysis and process automation, leading to more effective planning and operational activity.
- Human Capital and Culture: The importance of staff qualification and training, as well as the need for cultural changes to adopt new practices within an organization.
- Economic Analysis and Investments: Using methodologies to assess economic benefits and well-thought-out investments in new technologies as key factors for optimizing maintenance management and increasing returns.
- Practical Examples and Lessons: Analyzing successful and unsuccessful industry cases demonstrates the importance of strategic approaches and technological innovations for achieving operational success.
Industry Changes and Future Perspectives
- Technological Transformation: With the growing influence of digital technologies, the industry expects ongoing integration of IoT, AI, and machine learning in maintenance management. These technologies will play a key role in continuously improving efficiency and enabling companies to quickly adapt to emerging opportunities.
- Environmental Sustainability: In the context of global environmental concerns, the future of maintenance management will focus on environmentally sustainable practices, reducing waste, and optimizing resources.
- Globalization and Competitiveness: With ongoing globalization, companies need to enhance their operational flexibility and competitiveness. This means implementing globally coordinated maintenance strategies and integrating best practices from various regions.
- Personalization and Specific Solutions: Companies will need to create increasingly personalized solutions for their individual needs. This requires implementing technologies that allow for more detailed and effective management of resources and processes.
- Focus on the Human Factor: Despite technological advancements, human capabilities will remain central to successful maintenance management. Training staff and developing leadership will continue to play an important role in addressing more complex challenges.
Conclusion
The future of maintenance management is filled with challenges but also great opportunities for innovation and sustainable development. Through strategic planning, the appropriate use of technologies, and investment in human resources, companies can achieve long-term stability and competitiveness in this dynamic sector. Creating organizations that are ready to adapt and evolve with the changing environment will be essential for achieving success in the future.
Ready to improve your maintenance management? Contact us for a Fabrico CMMS demo!
Frequently Asked Questions (FAQ)
What is maintenance management?
Maintenance management is the systematic approach to planning, coordinating and controlling the activities involved in keeping equipment in good working order. Its purpose is to minimize downtime and optimize resources.
What are the main types of maintenance?
The main types of maintenance include reactive, preventive, predictive, and proactive maintenance. Each has its own advantages and can be used depending on the needs and conditions of the enterprise.
How are technologies such as IoT and AI impacting maintenance management?
Technologies such as IoT (Internet of Things) and AI (Artificial Intelligence) significantly improve maintenance management by introducing automation, collecting and analyzing data in real time, and providing the ability to predict failures before they happen.
What are the benefits of implementing CMMS systems?
CMMS (Computerized Maintenance Management Systems) systems provide centralized management of maintenance activities, improve planning and coordination, optimize inventory, and facilitate reporting resulting in better operational efficiency.
What is the role of human factors in maintenance management?
The human factor remains a central part of maintenance management despite technological advances. Staff training and qualifications play a key role in the successful implementation of new technologies and strategies.
How to calculate the economic benefit of maintenance?
The economic benefit of maintenance can be calculated through various methodologies, such as cost-benefit analysis (CBA), life cycle analysis (LCCA), and return on investment (ROI). These approaches help evaluate the long-term effectiveness of maintenance strategies.