What is Factory Scheduled Maintenance?
Factory scheduled maintenance, also known as preventive maintenance, is a planned and proactive maintenance strategy designed to keep equipment in optimal working condition. It goes beyond simply fixing things when they break. Instead, it focuses on performing routine tasks at specific intervals to prevent failures before they occur.
This approach is crucial for preventing unexpected equipment failures, optimizing performance, and extending the life of machinery. Unlike reactive maintenance (fixing equipment only when it breaks down), scheduled maintenance is proactive, aiming to keep operations running smoothly and efficiently.
Common Maintenance Tasks:
Typical tasks involved in factory scheduled maintenance include:
- Inspections: Regularly checking equipment for signs of wear, damage, or malfunction.
- Lubrication: Applying lubricants to moving parts to reduce friction and prevent wear.
- Parts Replacement: Replacing worn or damaged components before they cause major failures.
- System Calibrations: Ensuring equipment is calibrated correctly to maintain accuracy and performance.
- Cleaning: Removing dirt, debris, and contaminants that can affect equipment performance.
- Testing: Conducting performance tests to ensure equipment is operating within specified parameters.
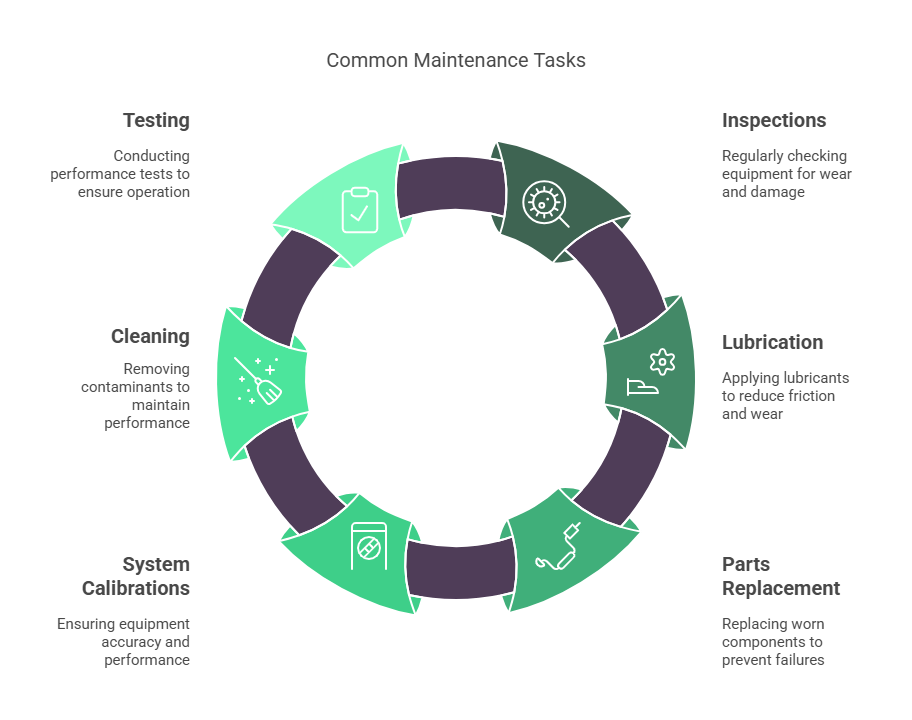
Recommended Intervals:
The frequency of maintenance tasks is typically determined by a combination of factors, including:
- Manufacturer Guidelines: Equipment manufacturers often provide recommended maintenance schedules and procedures.
- Usage Patterns: Equipment that is used more frequently or under harsh conditions may require more frequent maintenance.
- Operational Environments: The environment in which equipment operates (e.g., temperature, humidity, dust levels) can affect maintenance intervals.
- Historical Data: Analyzing past maintenance records can help identify patterns and optimize maintenance schedules.
Reliability-Centered Maintenance (RCM) can be used to optimize maintenance tasks and intervals based on equipment criticality.