Having mentioned just a few of the benefits of implementing a system maintenance plan, we will now delve into the steps involved in doing so. Although some organisations may already follow their own procedures, the steps outlined below are a great starting point for maintenance managers looking to improve productivity, performance and efficiency.
1. Identification of Problematic Areas
Organisations purchase equipment and machinery at different stages of the business life cycle. Often, when an organisation grows, it needs additional assets to make up for increasing production demand. What is important to note is that some of these assets may be new while others may be used or second-hand.
Each one comes with its own warranty and maintenance instructions. Furthermore, each asset has its own life span, such as the number of rotations, quantity of output, lubrication requirements, etc.
Perhaps more importantly, each team needs to maintain assets via their own individual maintenance schedule. It is set at regular intervals to ensure fewer malfunctions and less downtime. This is where maintenance managers should perform an audit of machines that perform well and those that do not, as well as regular inspections, to build an effective plan for your business.
Once such an audit is done, it is easier to work out what type of maintenance schedule to place each asset on and at what frequency it should be maintained. That’s why identifying problem areas right from the start is so essential.
Doing so will give maintenance managers the right information they need to address maintenance tasks as and when they are needed. This way, the production facility operates like a well-oiled machine with well-functioning moving parts that work in perfect sync with each other.
2. Prioritisation of Critical Tasks
Unfortunately, emergency repairs, as part of reactive maintenance, are a frequent occurrence in production processes because, no matter how well a maintenance schedule is planned, some unexpected problems and equipment breakdowns can arise without prior notice.
Although maintenance managers and crews can spend time planning for these, such events are unforeseeable. However, that doesn’t mean that there should be no maintenance plan or preventive maintenance programme. In fact, it is possible to prioritise different tasks to ensure the smooth operation of the production facility.
For example, one asset may break down and require attention or inspection while another may be undergoing routine maintenance. In such cases, a maintenance manager will need to determine how many and which physical and human resources to allocate to each task and the priority of the machine in the production pipeline.
Once such a determination is made, it’s also essential to do a cost-benefit analysis to see which machine’s faults should be addressed first so that there is optimal utilisation of resources at the plant. This action also ensures that processes are interrupted for as short a time as possible to avoid costly and lengthy downtime.
Want to learn more about maintenance, repair and operations in manufacturing? Read our detailed MRO guide.
3. Creation of a Preventive Maintenance (PM) Schedule
After critical tasks have been prioritised, it’s important to create a preventive maintenance (PM) schedule. A PM schedule is a timetable that gives an instant bird’s eye view of which assets need to be maintained and at what intervals.
Such a schedule answers pressing questions such as:
- How much skilled labour needs to be allocated to the task at hand?
- How long should the expected maintenance task take on average?
- Which spare parts should be used from inventory and storage alongside their associated costs?
Ideally, there should be a fine balance that’s struck between over-maintenance and under-maintenance.
Over-maintenance means allocating too many resources to a maintenance task for too many of the assets under management.
Under-maintenance, on the other hand, deals with not maintaining your piece of equipment sufficiently, meaning fewer human and physical resources are allocated to the maintenance task. Consequently, this can result in significant losses, production defects, quality control issues and costly downtime.
Designing a schedule for your preventive maintenance services should also involve grouping similar assets together, putting similar teams on one task or even ensuring that similar work is done on different machines. This can save teams a lot of time and will also ensure that labour and resources are optimally distributed and utilised, while reducing downtime through regular maintenance.
4. Optimisation of Spare Parts Inventory Management
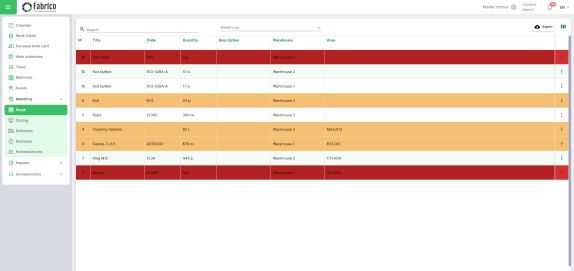
A great maintenance plan example will also consider optimising the management of spare parts inventory. Inventory is the lifeblood of any production process because it is necessary for the right spare parts to be available and easily accessible at the right time for maintenance crews to use.
However, maintaining track of inventory can be a challenging task. This is where a computerised maintenance management system (CMMS) outperforms any competing offering because it enables spare parts inventory management processes that are smooth and seamless.
When each new spare part is recorded in a centralised and digital inventory repository system, these spare parts are then accurately organised and accounted for. This ensures they are in excellent working condition, and there’s less room for leaks and wastage.
In addition, it’s possible to carry out efficient maintenance on time every time as a maintenance technician will not need to wait for spare parts to arrive. Thus, time is saved and downtime is minimised.
5. Monitoring and Analysis of Performance Metrics
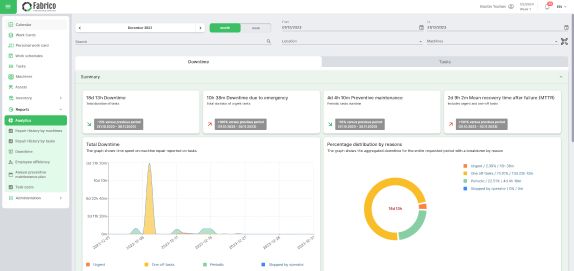
Finally, your maintenance plan should be backed by figures or maintenance metrics that illustrate the level of your efforts. For example, with CMMS maintenance software at your side, it’s possible to measure, monitor and analyse your performance metrics so that you can make informed decisions about your future maintenance efforts.
Often, with CMMS software at your fingertips, you’re able to establish benchmarks against which to monitor your performance. This can also help you make adjustments, where necessary, to simplify your maintenance efforts even further.
Introducing these kinds of efficiencies into your production processes through data-driven insights is a great way to reduce unnecessary costs and keep the organisation lean without the leakage of valuable resources.