Definition and Importance:
Preventive maintenance (PM) involves scheduled inspections, servicing, and repairs on equipment at predetermined intervals to prevent breakdowns and ensure optimal performance. It’s a proactive strategy, rather than waiting for something to fail. Implementing PM offers:
- Reduced Downtime: Preventing equipment failures minimizes production disruptions and maximizes uptime.
- Extended Equipment Lifespan: Regular maintenance prolongs the lifespan of your assets, reducing the need for costly replacements.
- Improved Safety: Ensuring equipment is in good working order reduces the risk of accidents and injuries.
- Cost Savings: Proactive maintenance is generally cheaper than reactive maintenance, yielding significant cost savings.
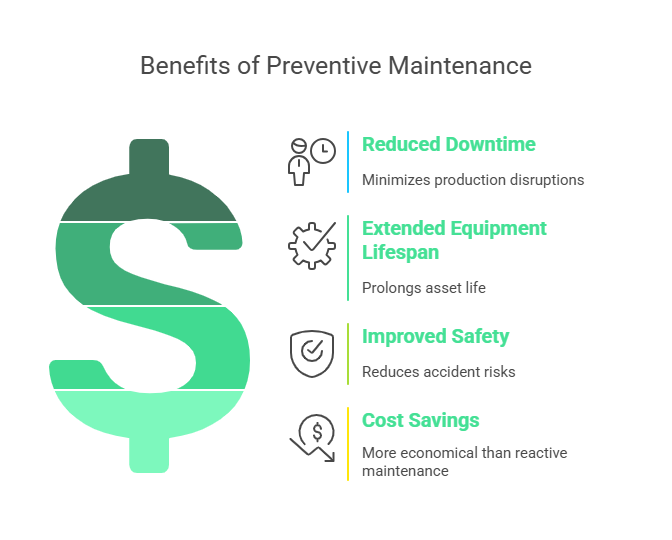
Challenges of Reactive Maintenance:
Relying solely on reactive maintenance (fixing equipment only after it breaks down) creates numerous challenges:
- Unplanned Downtime: Unexpected failures disrupt production and impact delivery schedules.
- Increased Costs: Emergency repairs are often more expensive than scheduled maintenance.
- Shorter Lifespan: Neglecting maintenance leads to premature wear and tear, shortening equipment life.
- Safety Hazards: Unexpected failures can lead to safety risks and potential accidents.
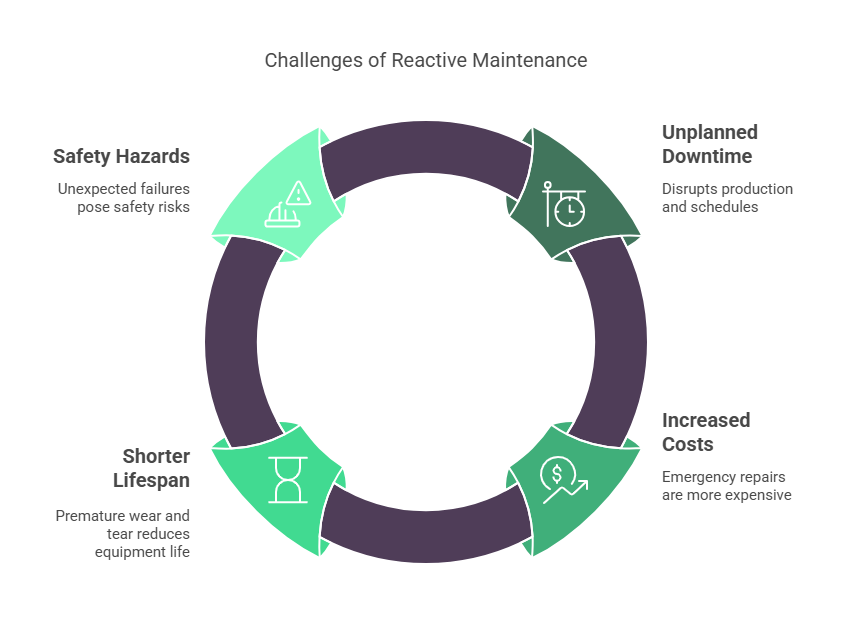