Managing the work order process can be daunting. It requires exceptional attention to detail and strong organisational skills. Here are six key steps for how to manage jobs efficiently and effectively.
1. Identifying maintenance tasks
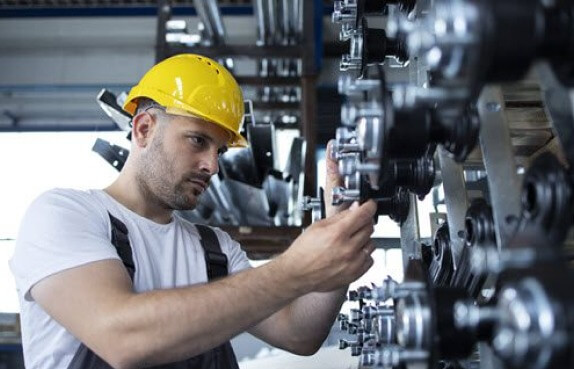
The world of manufacturing operations predominantly relies on machines. These need to be maintained regularly for several reasons. Firstly, to ensure that expensive equipment’s warranty remains valid. Secondly, maintenance helps to prevent costly downtime and a slowdown or halt in operations.
In most cases, maintenance managers deal with either unplanned or planned maintenance tasks. Unplanned maintenance is akin to a knee-jerk approach and is reactive. In other words, maintenance is carried out when a machine breaks down and an emergency work order is issued. This is also known as a corrective maintenance work order.
When it comes to planned maintenance, it is carried out proactively or before a machine malfunctions to ensure that all machinery operates smoothly. Since preventive maintenance as part of planned maintenance is one of the main maintenance activities, this is what we’ll focus on.
With this maintenance type, the process of managing tasks begins by identifying what maintenance tasks need to be carried out before a due date. For example, some maintenance tasks may be quite small and include things such as changing oil or lubricants, which can take around 20 minutes.
In other cases, a preventive maintenance task may take place across multiple facilities over several weeks and is, therefore, more time consuming and larger in scope. Identifying these maintenance tasks before an error or breakdown occurs is the first step in the process.
2. Submitting work requests
The second step after maintenance tasks have been identified is to create work order requests. This is done before the work order is created in step three, which is discussed next.
These requests are submitted (usually by machine operators and/or other team members) for review and approval. They can be a part of a regularly scheduled preventive maintenance task or a broader organisational audit.
When submitted for review, these work requests are analysed in terms of scope and details to determine the task's feasibility.
After this, the responsible team member determines what personnel and resources are required to complete the task. If approved, a work request is then converted to a work order.
3. Creating work orders
Creating work orders is the third step in the job process flow. When a work request is finalised and approved, it signals that there is sufficient manpower and resources for the maintenance task to be carried out.
In this creation process, an appointed member of your maintenance team or a supervisor is then responsible for allocating the materials, equipment and staff that will be required to finalise the job. This requires the task to be thoroughly set out.
All the necessary details of the jobs should be included, in addition to the priority level, deadline for completion, resources and materials to be used, which machine or asset will be worked on and who will be responsible.
To streamline the process, work order software helps eliminate unnecessary paperwork and digitises the process through task templates, which determine what type of work order needs to be carried out.
As such, when you have created a new work order and you want to submit it, the relevant team member will receive a notification (often on their smartphone or tablet) so that they know what they need to do, by when and how.
In addition, supervisors can use reminders after trigger-based events occur to schedule and create multiple jobs for their team.
4. Distributing and completing work orders
One of the major benefits of using a CMMS for your process is that you can submit a work task to the right team members. This is essential because each specialist may have different levels of qualifications and training.
Some may be well-suited to more regular maintenance tasks, while others may be more experienced and capable of handling more complex jobs. Strategically assigning tasks through a CMMS is one of the best ways to streamline your processes. That’s because this is done by automatically notifying the relevant person through a mobile or email notification received on their smartphones.
Furthermore, when you know what the capabilities and skill levels of your team are, you can assign those with lower levels of expertise to receive more training during quiet times. You can also onboard them to take on tasks with greater levels of complexity later on to create a constantly evolving workforce.
Once a team member is assigned to a job and they’ve been notified, they then get to work on it within the parameters set out in the specific job order. They should also pay attention to the time frame for the task’s completion, as work orders may have specific deadlines, and note any attached documentation, files or images. The latter can assist them in completing the job on schedule and within budget.
5. Documenting and closing work orders
The next step is to document and close the task. The reason behind this is simple. Documenting helps to note which processes were used, review previous solutions, build asset histories, work according to the organisation’s best practices and to prepare for audits.
Documentation also helps identify if any critical steps were missed to help future technicians know what challenge they are dealing with. After documentation is completed, the task may be considered closed.
This will signal to the relevant parties in your organisation that the order is ready. As such, accounts and financial teams can prepare invoices, if necessary, and ensure compliance requirements are met.
6. Reviewing and analysing work orders
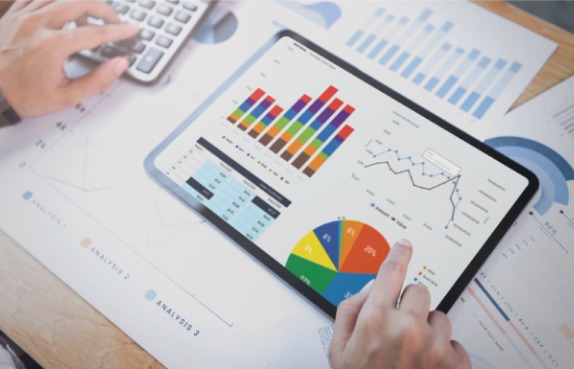
Scheduled jobs should be reviewed and analysed for many reasons. It’s about capturing valuable information from each order so that you can identify patterns, look for challenging areas and try to optimise your processes.
This can easily be done through work order management software, which gathers data from every work order, allowing you to create reports and study the insights that the data shows you. Ultimately, this will help with decision-making processes to introduce greater efficiencies in your preventive maintenance procedures.
When you study your work orders, you’ll also be able to ensure your machines are in perfect working order and that there is uniformity in terms of how the maintenance work was performed.